ඇඹරුම් තැටි විවිධ කර්මාන්තවල ප්රධාන කාර්යභාරයක් ඉටු කරයි, ද්රව්ය හැඩගැස්වීම සහ නිම කිරීම පහසු කරයි. කෙසේ වෙතත්, වෙනත් ඕනෑම මෙවලමක් මෙන්, ඒවායේ කාර්යක්ෂමතාවයට සහ ක්රියාකාරිත්වයට බාධා කළ හැකි ගැටළු වලින් ඒවා නිදහස් නොවේ. මෙම ලිපියෙන්, අපි පොදු ඇඹරුම් තැටි ගැටළු පිළිබඳව සොයා බලමු, ඒවායේ මූල හේතු ගවේෂණය කරන්නෙමු, සහ බාධාවකින් තොරව වැඩ ප්රවාහයක් සඳහා ඵලදායී විසඳුම් ලබා දෙන්නෙමු.
හැඳින්වීම
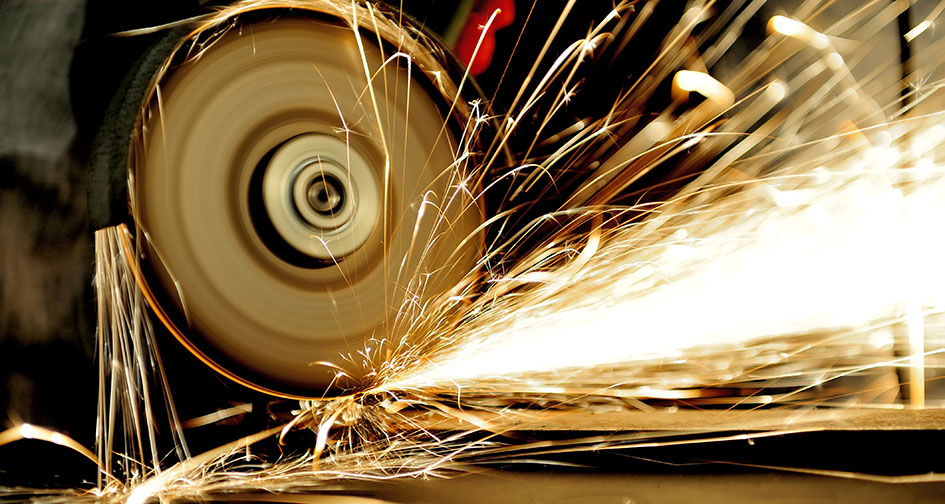
ඇඹරුම් තැටි විවිධ කර්මාන්තවල මූලික කාර්යභාරයක් ඉටු කරයි, ද්රව්ය ඉවත් කිරීම, හැඩගැස්වීම සහ නිම කිරීමේ ක්රියාවලීන් සඳහා අත්යවශ්ය මෙවලම් ලෙස සේවය කරයි. ඒවායේ නිර්වචනය, කර්මාන්ත හරහා වැදගත්කම සහ මුහුණ දෙන පොදු ගැටළු අවබෝධ කර ගැනීම ඒවායේ භාවිතය ප්රශස්ත කිරීම සහ කාර්යක්ෂම මෙහෙයුම් සහතික කිරීම සඳහා ඉතා වැදගත් වේ.
A. ඇඹරුම් තැටි අර්ථ දැක්වීම
ඇඹරුම් තැටි යනු ද්රව්ය මතුපිට කැපීම, ඇඹරීම හෝ ඔප දැමීම සඳහා යන්ත්රෝපකරණ ක්රියාවලීන්හි භාවිතා කරන උල්ෙල්ඛ මෙවලම් වේ. මෙම තැටි සාමාන්යයෙන් ආධාරක ද්රව්යයකට බන්ධනය වූ උල්ෙල්ඛ අංශු වලින් සමන්විත වන අතර, අතිරික්ත ද්රව්ය ඉවත් කිරීමට, මතුපිට සුමට කිරීමට හෝ දාර තියුණු කිරීමට හැකි භ්රමණය වන මෙවලමක් නිර්මාණය කරයි. ඒවා විවිධ හැඩයන් සහ ප්රමාණවලින් පැමිණේ, ඒ සෑම එකක්ම නිශ්චිත යෙදුම් සඳහා නිර්මාණය කර ඇත.
B. විවිධ කර්මාන්තවල වැදගත්කම
ලෝහ වැඩ කර්මාන්තය:
ලෝහ නිෂ්පාදනය සහ නිෂ්පාදනයේදී, ලෝහ මතුපිට හැඩගැන්වීම, ඉවත් කිරීම සහ නිම කිරීම සඳහා ඇඹරුම් තැටි අත්යවශ්ය වේ. නිරවද්ය මානයන් සහ මතුපිට ගුණාත්මකභාවය ලබා ගැනීම සඳහා ඒවා සාමාන්යයෙන් කෝණ ඇඹරුම් යන්ත සමඟ භාවිතා වේ.
ඉදිකිරීම් කර්මාන්තය:
ඉදිකිරීම් වෘත්තිකයන් කොන්ක්රීට් මතුපිට සකස් කිරීම, රළු දාර සුමට කිරීම සහ ගල් සහ කොන්ක්රීට් වැනි ද්රව්යවල අඩුපාඩු ඉවත් කිරීම වැනි කාර්යයන් සඳහා ඇඹරුම් තැටි මත විශ්වාසය තබති.
මෝටර් රථ කර්මාන්තය:
මෝටර් රථ අංශයේ මුවහත් කිරීමේ මෙවලම්වල සිට ලෝහ සංරචක හැඩගැන්වීම සහ නිම කිරීම දක්වා කාර්යයන් සඳහා ඇඹරුම් තැටි අත්යවශ්ය වේ. ඒවා මෝටර් රථ කොටස්වල නිරවද්යතාවය සහ ගුණාත්මකභාවය සඳහා දායක වේ.
ලී වැඩ කර්මාන්තය:
ලී වැඩ කරන්නන් ලී මතුපිට හැඩගැන්වීම සහ සුමට කිරීම සඳහා ඇඹරුම් තැටි භාවිතා කරයි. මෙම තැටි අතිරික්ත ද්රව්ය ඉවත් කිරීම, හැඩතල පිරිපහදු කිරීම සහ තවදුරටත් නිම කිරීම සඳහා දැව සකස් කිරීම සඳහා ඵලදායී වේ.
සාමාන්ය නිෂ්පාදනය:
ඇඹරුම් තැටි විවිධ නිෂ්පාදන ක්රියාවලීන්හි යෙදීම් සොයා ගන්නා අතර එහිදී නිරවද්ය ද්රව්ය ඉවත් කිරීම අවශ්ය වන අතර එමඟින් උසස් තත්ත්වයේ සංරචක නිෂ්පාදනයට දායක වේ.
ඇ. මුහුණ දෙන පොදු ගැටළු
තැටි ඇඳීම සහ සීරීම:
අඛණ්ඩව භාවිතා කිරීම ඇඹරුම් තැටියේ ඇඳීමට සහ සීරීම් වලට හේතු විය හැකි අතර, එහි ක්රියාකාරිත්වයට බලපායි. කාර්යක්ෂමතාව පවත්වා ගැනීම සඳහා නිතිපතා පරීක්ෂා කිරීම සහ ප්රතිස්ථාපනය කිරීම අවශ්ය වේ.
අධික උනුසුම් වීම:
දීර්ඝ කාලයක් භාවිතා කිරීමේදී අධික ඝර්ෂණය හේතුවෙන් තැටිය අධික ලෙස රත් වීමට ඉඩ ඇති අතර එමඟින් එහි කල්පැවැත්මට සහ නිමි පෘෂ්ඨයේ ගුණාත්මක භාවයට බලපෑම් ඇති විය හැක. නිසි සිසිලන පියවර සහ වරින් වර විවේක ගැනීම අත්යවශ්ය වේ.
අවහිර වීම:
ඇඹරුම් තැටි මගින් ද්රව්යමය අපද්රව්ය එකතු විය හැකි අතර, ඒවායේ කාර්යක්ෂමතාව අඩු වේ. නිතිපතා පිරිසිදු කිරීම හෝ අවහිරතා වැළැක්වීමේ ලක්ෂණ සහිත තැටි තෝරා ගැනීම මෙම ගැටළුව වළක්වා ගැනීමට උපකාරී වේ.
කම්පනය සහ වෙව්ලීම:
අසමතුලිතතාවයන් හෝ අසමාන ඇඳීම් හේතුවෙන් කම්පනය හෝ සෙලවීම සිදුවිය හැකි අතර, එය නිමාවේ ගුණාත්මක භාවයට සහ ක්රියාකාරිත්වයේ ආරක්ෂාවට බලපායි. නිසි ස්ථාපනය සහ තුලනය ඉතා වැදගත් වේ.
වැරදි තැටි තේරීම:
නිශ්චිත ද්රව්යයක් හෝ යෙදුමක් සඳහා වැරදි ආකාරයේ ඇඹරුම් තැටියක් තෝරා ගැනීම අකාර්යක්ෂමතාවයට සහ විභව හානිවලට හේතු විය හැක. ද්රව්ය අනුකූලතාව මත පදනම්ව නිසි තේරීම අත්යවශ්ය වේ.
මෙම මෙවලම් මත යැපෙන කර්මාන්ත සඳහා ඇඹරුම් තැටි හා සම්බන්ධ නිර්වචනය, වැදගත්කම සහ විභව අභියෝග අවබෝධ කර ගැනීම අත්යවශ්ය වේ. පොදු ගැටළු විසඳීමෙන් සහ නිසි භාවිතය සහතික කිරීමෙන්, කර්මාන්තවලට අදාළ යෙදුම්වල ඇඹරුම් තැටිවල කාර්යක්ෂමතාව උපරිම කළ හැකිය.
ඇඹරුම් තැටි මත ඇඳීම සහ ඉරීම
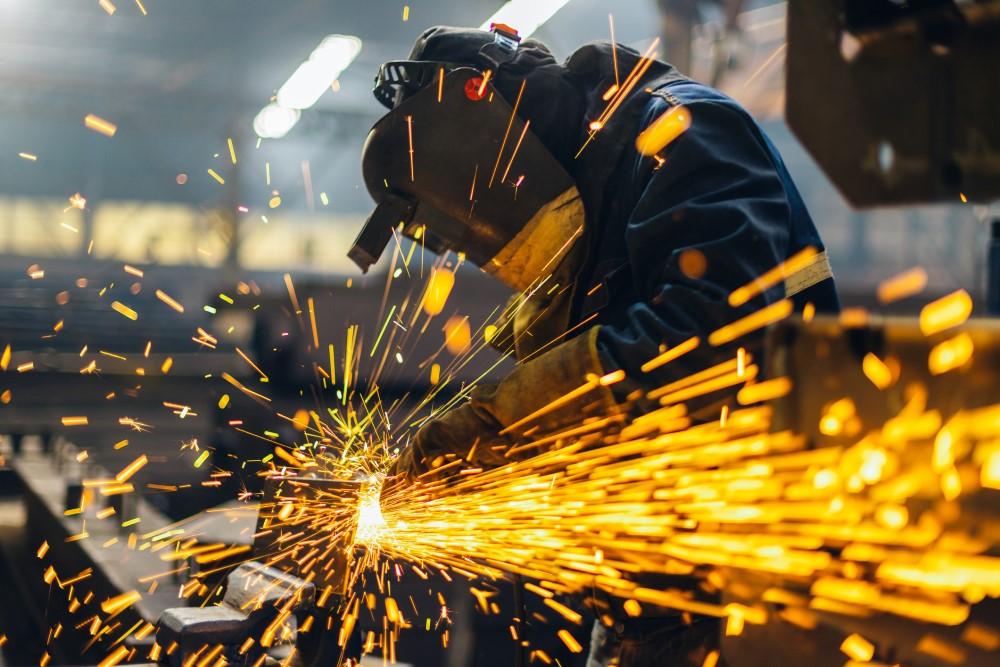
ඇඹරුම් තැටි විවිධ කර්මාන්තවල අත්යවශ්ය මෙවලම් වන අතර, ලෝහ නිෂ්පාදනයේ සිට කොන්ක්රීට් ඔප දැමීම දක්වා කාර්යයන් සඳහා අවශ්ය උල්ෙල්ඛ ලබා දෙයි. ඇඹරුම් තැටිවල ඇඳීමට සහ ඉරී යාමට දායක වන සාධක අවබෝධ කර ගැනීම, ඒවායේ ක්රියාකාරිත්වය ප්රශස්ත කිරීම සහ ආරක්ෂාව සහතික කිරීම සඳහා ඉතා වැදගත් වේ.
ද්රව්ය දෘඪතාව සහ සංයුතිය:
දෘඪතාවේ වෙනස්කම්:ඇඹරුම් තැටි විවිධ දෘඪතා මට්ටම් සහිත ද්රව්ය සමඟ ගැටේ. ලෝහ සහ කොන්ක්රීට් වැනි උල්ෙල්ඛ ද්රව්ය දෘඪතාවයෙන් සැලකිය යුතු ලෙස වෙනස් විය හැකිය. දෘඪ ද්රව්යවලට එරෙහිව අඛණ්ඩව ඇඹරීම ඇඳීම වේගවත් කරයි.
ද්රව්ය සංයුතිය:ඇඹරීමට ගන්නා ද්රව්යයේ උල්ෙල්ඛ මූලද්රව්ය පැවතීම ඇඹරුම් තැටියේ ගෙවී යාමට බලපෑම් කළ හැකිය. උල්ෙල්ඛ අංශු තැටිය ගෙවී යාම වේගවත් කළ හැකිය.
ඇඹරුම් පීඩනය සහ බලය:
අධික පීඩනය:ඇඹරුම් තැටිය මත අධික පීඩනය යෙදීමෙන් ඉක්මනින් ගෙවී යා හැක. තැටිය මත අනවශ්ය ආතතියක් ඇතිවීම වළක්වා ගැනීම සඳහා නිශ්චිත යෙදුම සඳහා නිර්දේශිත පීඩනය භාවිතා කිරීම අත්යවශ්ය වේ.
ප්රමාණවත් නොවන බලය: අනෙක් අතට, ප්රමාණවත් බලයක් නොමැතිකම දිගු වේලාවක් ඇඹරීමට හේතු විය හැකි අතර, අමතර ඝර්ෂණය සහ තාපය ජනනය කරමින්, ගෙවී යාමට දායක වේ.
තැටියේ ගුණාත්මකභාවය සහ සංයුතිය:
උල්ෙල්ඛ ද්රව්යවල ගුණාත්මකභාවය:ඇඹරුම් තැටියේ භාවිතා කරන උල්ෙල්ඛ ද්රව්යයේ ගුණාත්මකභාවය එහි ආයු කාලය සැලකිය යුතු ලෙස බලපායි. උසස් තත්ත්වයේ උල්ෙල්ඛ ද්රව්ය ඇඳීමට ප්රතිරෝධී වන අතර තියුණු බව දිගු කාලයක් පවත්වා ගනී.
බන්ධන නියෝජිතයා:උල්ෙල්ඛ අංශු එකට තබා ගන්නා බන්ධන කාරකය තීරණාත්මක කාර්යභාරයක් ඉටු කරයි. හොඳින් නිර්මාණය කරන ලද බන්ධන කාරකයක් තැටියේ කල්පැවැත්ම වැඩි දියුණු කරයි.
වැඩ පරිසර කොන්දේසි:
උෂ්ණත්වය:ඇඹරීමේදී ජනනය වන ඉහළ උෂ්ණත්වයන් තැටියේ සංයුතියට බලපෑම් කළ හැකිය. අධික තාපය බන්ධන කාරකය දුර්වල කරන අතර ගෙවී යාම වේගවත් කරයි.
තෙතමනය සහ දූෂක:වැඩ කරන පරිසරයේ තෙතමනය හෝ දූෂක ද්රව්යවලට නිරාවරණය වීම ඇඹරුම් තැටියේ අඛණ්ඩතාවයට බලපෑ හැකි අතර, එය වේගවත් ඇඳීමට හේතු වේ.
ක්රියාකරු තාක්ෂණය:
නිසි තාක්ෂණය:ක්රියාකරුගේ කුසලතාව සහ තාක්ෂණය අත්යවශ්ය වේ. වැරදි කෝණවලින් ඇඹරීම හෝ අධික බලයක් භාවිතා කිරීම වැනි නුසුදුසු භාවිතයන් අසමාන ඇඳීමට දායක විය හැකි අතර තැටියේ ආයු කාලය අඩු කරයි.
නිතිපතා පරීක්ෂණ:ක්රියාකරුවන් විසින් ඇඹරුම් තැටියට හානි හෝ ගෙවී යාමේ සලකුණු තිබේදැයි නිතිපතා පරීක්ෂා කළ යුතුය. නිශ්චිත ස්ථානයකට වඩා ගෙවී යන තැටි ඉක්මනින් ප්රතිස්ථාපනය කළ යුතුය.
තැටි ප්රමාණය සහ RPM අනුකූලතාව:
නිවැරදි ප්රමාණය:ඇඹරුම් යන්තය සඳහා නිවැරදි තැටි ප්රමාණය භාවිතා කිරීම ඉතා වැදගත් වේ. වැරදි ප්රමාණයේ තැටි අසමාන ලෙස ගෙවී යා හැකි අතර ආරක්ෂිත අවදානම් ඇති කළ හැකිය.
RPM අනුකූලතාව:ඇඹරුම් තැටිය සඳහා නිර්දේශිත මිනිත්තුවකට විප්ලව (RPM) පිළිපැදීම ප්රශස්ත ක්රියාකාරිත්වය සහතික කරන අතර අකාලයේ ගෙවී යාම වළක්වයි.
නිතිපතා නඩත්තු කිරීම, නිර්දේශිත මෙහෙයුම් තත්ත්වයන් පිළිපැදීම සහ කාර්යය සඳහා නිවැරදි ඇඹරුම් තැටිය තෝරා ගැනීම, ගෙවී යාම සහ ඉරීම අවම කිරීම සඳහා අත්යවශ්ය පිළිවෙත් වේ. ගෙවී යාමට බලපාන සාධක තේරුම් ගැනීමෙන්, ක්රියාකරුවන්ට ඇඹරුම් තැටිවල ආයු කාලය සහ කාර්යක්ෂමතාව වැඩි දියුණු කළ හැකි අතර, ආරක්ෂිත සහ වඩාත් ඵලදායී ඇඹරුම් මෙහෙයුම් සඳහා දායක විය හැකිය.
අසමාන ඇඹරීම
අසමාන ඇඹරීම යනු ඇඹරීමට ලක් කර ඇති මතුපිට ස්ථාවර හා සුමට නිමාවක් ලබා නොගන්නා තත්වයයි. මෙම ගැටළුව විවිධ හේතූන් මත මතු විය හැකි අතර වැඩ කොටසෙහි ගුණාත්මක භාවයට බලපෑම් කළ හැකිය. අසමාන ඇඹරීමට දායක වන පොදු සාධක සහ විභව විසඳුම් මෙන්න:
වැරදි ඇඹරුම් රෝද තේරීම:
විසඳුමක්:ඇඹරුම් රෝදය ඇඹරීමට නියමිත ද්රව්යයට සුදුසු බව සහතික කර ගන්න. විවිධ ද්රව්ය සඳහා නිශ්චිත උල්ෙල්ඛ ගුණාංග අවශ්ය වේ. යෙදුම සඳහා නිවැරදි රෝද වර්ගය, ග්රිට් ප්රමාණය සහ බන්ධනය තෝරන්න.
නුසුදුසු රෝද ඇඳීම:
හේතුව:නිසි ලෙස සකස් නොකළ ඇඹරුම් රෝදයක් අසමාන ඇඳීමට සහ අකාර්යක්ෂම කැපීමට හේතු විය හැක.
විසඳුමක්:ඇඹරුම් රෝදයේ හැඩය පවත්වා ගැනීමට සහ එකතු වී ඇති සුන්බුන් ඉවත් කිරීමට නිතිපතා එය සැරසීම. නිසි ලෙස සැරසීම මඟින් ස්ථාවර කැපුම් මතුපිටක් සහතික කෙරේ.
ප්රමාණවත් නොවන ඇඹරුම් තරලය හෝ සිසිලනකාරකය:
හේතුව:ඇඹරුම් තරලය ප්රමාණවත් නොවීම හෝ අනිසි ලෙස භාවිතා කිරීම නිසා ඝර්ෂණය සහ තාපය වැඩි විය හැකි අතර, එය අසමාන ඇඹරීමට හේතු වේ.
විසඳුමක්:තාපය විසුරුවා හැරීමට සහ ඝර්ෂණය අඩු කිරීමට සුදුසු ඇඹරුම් තරලයක් හෝ සිසිලනකාරකයක් භාවිතා කරන්න. ඒකාකාර ප්රතිඵල ලබා ගැනීම සඳහා නිසි සිසිලනය අත්යවශ්ය වේ.
වැරදි ඇඹරුම් පරාමිතීන්:
හේතුව:අධික වේගය, පෝෂණ අනුපාතය හෝ කැපුම් ගැඹුර වැනි වැරදි ඇඹරුම් පරාමිතීන් භාවිතා කිරීම අසමාන ඇඹරීමට හේතු විය හැක.
විසඳුමක්:ද්රව්ය හා යෙදුම් අවශ්යතා අනුව ඇඹරුම් පරාමිතීන් සකස් කරන්න. ප්රශස්ත සැකසුම් සඳහා නිෂ්පාදක නිර්දේශ වෙත යොමු වන්න.
ගෙවී ගිය ඇඹරුම් රෝදය:
හේතුව:ගෙවී ගිය ඇඹරුම් රෝදයක් ස්ථාවර කැපුම් මතුපිටක් ලබා නොදිය හැකි අතර, එහි ප්රතිඵලයක් ලෙස අසමාන ඇඹරීමක් සිදු වේ.
විසඳුමක්:භාවිතා කළ හැකි ආයු කාලය අවසන් වූ විට ඇඹරුම් රෝදය ප්රතිස්ථාපනය කරන්න. ගෙවී යාමේ සලකුණු සඳහා නිතිපතා රෝදය පරීක්ෂා කරන්න.
අසමාන පීඩනය හෝ ආහාර අනුපාතය:
හේතුව:ඇඹරීමේදී අසමාන පීඩනය හෝ නොගැලපෙන ආහාර අනුපාතයන් අක්රමවත් ද්රව්ය ඉවත් කිරීමට හේතු විය හැක.
විසඳුමක්:වැඩ කොටස පුරා ඒකාකාර පීඩනයක් යොදන්න සහ ස්ථාවර පෝෂණ අනුපාතයක් පවත්වා ගන්න. ක්රියාකරු කුසලතාව සහ විස්තර කෙරෙහි අවධානය ඉතා වැදගත් වේ.
යන්ත්ර ගැටළු:
හේතුව:ඇඹරුම් යන්ත්රයේ ඇති යාන්ත්රික ගැටළු, එනම් නොගැලපීම හෝ ස්පින්ඩලයේ ගැටළු, අසමාන ඇඹරීමට හේතු විය හැක.
විසඳුමක්:ඇඹරුම් යන්ත්රයේ නිතිපතා නඩත්තු පරීක්ෂාවන් සිදු කරන්න. නිසි ක්රියාකාරීත්වය සහතික කිරීම සඳහා ඕනෑම යාන්ත්රික ගැටළු වහාම විසඳන්න.
වැඩ කොටස් සවිකිරීම:
හේතුව:දුර්වල ලෙස සවි කර ඇති හෝ වැරදි ලෙස සකස් කර ඇති වැඩ කොටස් අසමාන ඇඹරීමට හේතු විය හැක.
විසඳුමක්:වැඩ කොටස නිසි ලෙස සවි කිරීම සහ පෙළගැස්වීම සහතික කරන්න. ඇඹරුම් ක්රියාවලියේදී චලනය වීම වැළැක්වීම සඳහා එය තදින් සවි කරන්න.
අසමාන ඇඹරීම ආමන්ත්රණය කිරීම සඳහා නිසි උපකරණ සැකසුම, නිවැරදි මෙහෙයුම් පරාමිතීන් සහ නිතිපතා නඩත්තු පිළිවෙත්වල එකතුවක් අවශ්ය වේ. ඇඹරුම් යෙදීම්වල උසස් තත්ත්වයේ සහ ස්ථාවර ප්රතිඵල ලබා ගැනීම සඳහා ගැටළු හඳුනාගෙන ඉක්මනින් නිවැරදි කිරීමට ක්රියාකරුවන් පුහුණු කළ යුතුය. නිතිපතා පරීක්ෂා කිරීම් සහ හොඳම පිළිවෙත් පිළිපැදීම ඇඹරුම් ක්රියාවලියේදී කාර්යක්ෂම හා ඒකාකාර ද්රව්ය ඉවත් කිරීමට දායක වේ.
අධික උනුසුම් ගැටළු
ඇඹරීමේදී අධික ලෙස රත් වීම ඇඹරුම් රෝදයේ සහ වැඩ කොටසෙහි ක්රියාකාරිත්වයට බලපාන පොදු ගැටළුවකි. අධික තාපය රෝද ආයු කාලය අඩුවීම, වැඩ කොටසට තාප හානි වීම සහ සමස්ත ඇඹරුම් කාර්යක්ෂමතාව අඩුවීම ඇතුළු විවිධ ගැටළු වලට හේතු විය හැක. අධික උනුසුම් ගැටළු විසඳීම සඳහා විය හැකි හේතු සහ විසඳුම් මෙන්න:
වැරදි ඇඹරුම් පරාමිතීන්:
හේතුව:අධික වේගය, පෝෂණ අනුපාතය හෝ කැපුම් ගැඹුර වැනි නුසුදුසු ඇඹරුම් පරාමිතීන් භාවිතා කිරීමෙන් අතිරික්ත තාපය ජනනය විය හැකිය.
විසඳුමක්:නිර්දේශිත පරාසය තුළ ඇඹරුම් පරාමිතීන් සකසන්න. ඇඹරීමට නියමිත ද්රව්යය මත පදනම්ව ප්රශස්ත සැකසුම් සඳහා නිෂ්පාදකයාගේ මාර්ගෝපදේශ බලන්න.
ප්රමාණවත් සිසිලනය හෝ ලිහිසිකරණය:
හේතුව:සිසිලනකාරකය හෝ ඇඹරුම් තරලය ප්රමාණවත් ලෙස භාවිතා නොකිරීම නිසා ඝර්ෂණය හා තාපය වැඩි විය හැක.
විසඳුමක්:ඇඹරුම් ක්රියාවලියේදී ප්රමාණවත් සිසිලනකාරකයක් හෝ ලිහිසි තෙල් සැපයුමක් සහතික කර ගන්න. නිසි සිසිලනය තාපය විසුරුවා හැරීමට සහ තාප හානිය වළක්වයි.
වැරදි රෝද තේරීම:
හේතුව:ඇඹරීමට නියමිත ද්රව්ය සඳහා නුසුදුසු පිරිවිතරයන් සහිත ඇඹරුම් රෝදයක් තෝරා ගැනීම අධික උනුසුම් වීමට හේතු විය හැක.
විසඳුමක්:නිශ්චිත යෙදුම සඳහා නිවැරදි උල්ෙල්ඛ වර්ගය, ග්රිට් ප්රමාණය සහ බන්ධනය සහිත ඇඹරුම් රෝදයක් තෝරන්න. රෝදය ද්රව්යයට ගැලපීම තාප උත්පාදනය අවම කරයි.
වැඩ කොටස් ද්රව්ය ගැටළු:
හේතුව:සමහර ද්රව්ය, විශේෂයෙන් දුර්වල තාප සන්නායකතාවක් ඇති ද්රව්ය, ඇඹරීමේදී අධික ලෙස රත් වීමට වැඩි ප්රවණතාවක් දක්වයි.
විසඳුමක්:අඩු තාප සන්නායකතාවක් ඇති ද්රව්ය සඳහා ඇඹරුම් පරාමිතීන් සකස් කරන්න. තාප සංවේදී ද්රව්ය සඳහා නිර්මාණය කර ඇති විශේෂිත ඇඹරුම් රෝදයක් භාවිතා කිරීම සලකා බලන්න.
රෝද ඇඳීමේ ගැටළු:
හේතුව:ඇඹරුම් රෝදයේ අක්රමිකතා හෝ නුසුදුසු ඇඳුම් ඇඳීම අසමාන සම්බන්ධතා සහ තාපය ගොඩනැගීමට හේතු විය හැක.
විසඳුමක්:ඇඹරුම් රෝදයේ හැඩය පවත්වා ගැනීමට සහ ඕනෑම ඔප දැමීමක් හෝ සමුච්චිත සුන්බුන් ඉවත් කිරීමට නිතිපතා එය සැරසීම. නිසි ලෙස සැරසුණු රෝද ස්ථාවර ඇඹරුම් කාර්ය සාධනය සහතික කරයි.
ප්රමාණවත් යන්ත්ර නඩත්තුවක් නොමැතිකම:
හේතුව:දුර්වල ලෙස නඩත්තු කරන ලද ඇඹරුම් යන්ත්ර අධික උනුසුම් ගැටළු වලට දායක විය හැකිය.
විසඳුමක්:සිසිලන පද්ධති පරීක්ෂා කිරීම, රෝද ඇඳීමේ උපකරණ පරීක්ෂා කිරීම සහ නිසි පෙළගැස්ම සහතික කිරීම ඇතුළුව ඇඹරුම් යන්ත්රයේ නිතිපතා නඩත්තු කටයුතු සිදු කරන්න. ඕනෑම යාන්ත්රික ගැටළු වහාම විසඳන්න.
රෝද සිසිලන ප්රවාහය ප්රමාණවත් නොවීම:
හේතුව:ඇඹරුම් කලාපයට සිසිලනකාරක ප්රවාහය ප්රමාණවත් නොවීම නිසා තාපය විසුරුවා හැරීම අඩු විය හැකිය.
විසඳුමක්:සිසිලනකාරක බෙදා හැරීමේ පද්ධතිය පරීක්ෂා කර ප්රශස්ත කරන්න. සිසිලන කාර්යක්ෂමතාව පවත්වා ගැනීම සඳහා සිසිලනකාරකය ඇඹරුම් කලාපයට ඵලදායී ලෙස ළඟා වන බව සහතික කර ගන්න.
අධික ඇඹරුම් කාලය:
හේතුව:විවේකයකින් තොරව දීර්ඝ කාලයක් ඇඹරුම් සැසි පැවැත්වීම තාපය ගොඩනැගීමට දායක විය හැක.
විසඳුමක්:අධික තාප සමුච්චය වීම වැළැක්වීම සඳහා වරින් වර ඇඹරීම ක්රියාත්මක කර විවේක ගැනීමට ඉඩ දෙන්න. මෙම ප්රවේශය විශාල හෝ අභියෝගාත්මක ඇඹරුම් කාර්යයන් සඳහා විශේෂයෙන් වැදගත් වේ.
ඇඹරීමේදී අධික උනුසුම් ගැටළු විසඳීම සඳහා නිසි උපකරණ සැකසුම, සුදුසු ඇඹරුම් පරාමිතීන් සහ නිතිපතා නඩත්තු පිළිවෙත් ඇතුළත් පුළුල් ප්රවේශයක් අවශ්ය වේ. ප්රශස්ත ක්රියාකාරිත්වය, දීර්ඝ මෙවලම් ආයු කාලය සහ උසස් තත්ත්වයේ ප්රතිඵල සහතික කිරීම සඳහා ක්රියාකරුවන් ඇඹරුම් ක්රියාවලියේදී තාප උත්පාදනය නිරීක්ෂණය කර පාලනය කළ යුතුය.
කම්පන ගැටළු
ඇඹරුම් මෙහෙයුම් අතරතුර අධික කම්පනය විවිධ ගැටළු වලට තුඩු දිය හැකි අතර, මතුපිට ගුණාත්මකභාවය අඩුවීම, මෙවලම් ගෙවී යාම වැඩි වීම සහ ඇඹරුම් යන්ත්රයට සිදුවිය හැකි හානි ඇතුළු ගැටළු ඇති විය හැක. නිරවද්ය හා කාර්යක්ෂම ඇඹරුම් ක්රියාවලීන් සාක්ෂාත් කර ගැනීම සඳහා කම්පන ගැටළු විසඳීම ඉතා වැදගත් වේ. කම්පන ගැටළු අවම කිරීම සඳහා විය හැකි හේතු සහ විසඳුම් මෙන්න:
අසමාන රෝද ඇඳීම:
හේතුව:ඇඹරුම් රෝදය අක්රමවත් ලෙස ගෙවී යාම නිසා වැඩ කොටස සමඟ අසමාන සම්බන්ධතාවක් ඇති විය හැකි අතර එමඟින් කම්පන ඇති විය හැක.
විසඳුමක්:ස්ථාවර හා පැතලි මතුපිටක් පවත්වා ගැනීම සඳහා ඇඹරුම් රෝදය නිතිපතා පරීක්ෂා කර අඳින්න. නිසි රෝද නඩත්තුව කම්පන අවම කිරීමට උපකාරී වේ.
අසමතුලිත ඇඹරුම් රෝදය:
හේතුව:ඇඹරුම් රෝදයේ අසමතුලිතතාවයක්, අසමාන ඇඳීම් හෝ නිෂ්පාදන දෝෂ නිසා, කම්පනයට හේතු විය හැක.
විසඳුමක්:රෝද සමතුලිතකාරකයක් භාවිතයෙන් ඇඹරුම් රෝදය සමතුලිත කරන්න. සමතුලිතතාවය බර ඒකාකාරව බෙදා හැරීම සහතික කරන අතර ක්රියාත්මක වන විට කම්පන අඩු කරයි.
ප්රමාණවත් නොවන යන්ත්ර ක්රමාංකනය:
හේතුව:රෝද ස්පින්ඩලය හෝ වැඩ මේසය වැනි යන්ත්ර සංරචක දුර්වල ලෙස ක්රමාංකනය කිරීම හෝ වැරදි ලෙස පෙළගැස්වීම කම්පන වලට දායක විය හැකිය.
විසඳුමක්:නිසි ක්රියාකාරීත්වය සහතික කිරීම සඳහා යන්ත්ර සංරචක නිතිපතා ක්රමාංකනය කර පෙළගස්වන්න. යන්ත්ර සැකසීම සහ පෙළගැස්ම සඳහා නිෂ්පාදකයාගේ මාර්ගෝපදේශ අනුගමනය කරන්න.
වැඩ කොටස අසමතුලිතතාවය:
හේතුව:අසමාන හෝ නුසුදුසු ලෙස සුරක්ෂිත කර ඇති වැඩ කොටස අසමතුලිතතාවයක් ඇති කළ හැකි අතර කම්පන ඇති කළ හැකිය.
විසඳුමක්:වැඩ කොටස නිසි ලෙස සුරක්ෂිත කරන්න, එය ඒකාකාරව ස්ථානගත කර ඇති බවත් කලම්ප කර ඇති බවත් සහතික කර ගන්න. ඇඹරුම් ක්රියාවලිය ආරම්භ කිරීමට පෙර ඕනෑම අසමතුලිතතා ගැටළු විසඳන්න.
වැරදි රෝද තේරීම:
හේතුව:නුසුදුසු පිරිවිතරයන් සහිත ඇඹරුම් රෝදයක් භාවිතා කිරීමෙන් කම්පන ඇති විය හැක.
විසඳුමක්:ඇඹරීමට නියමිත ද්රව්යය සඳහා නිවැරදි උල්ෙල්ඛ වර්ගය, ග්රිට් ප්රමාණය සහ බන්ධනය සහිත ඇඹරුම් රෝදයක් තෝරන්න. යෙදුමට රෝදය ගැලපීම කම්පන අවම කරයි.
යන්ත්ර ඇඳීම සහ ඉරීම:
හේතුව:බෙයාරිං හෝ ස්පින්ඩල් වැනි ගෙවී ගිය හෝ හානි වූ යන්ත්ර සංරචක කම්පන වලට දායක විය හැක.
විසඳුමක්:ගෙවී ගිය යන්ත්ර කොටස් නිතිපතා පරීක්ෂා කර ප්රතිස්ථාපනය කරන්න. නිසි නඩත්තුව අධික කම්පන වැළැක්වීමට සහ ඇඹරුම් යන්ත්රයේ ආයු කාලය දීර්ඝ කිරීමට උපකාරී වේ.
ප්රමාණවත් නොවන සිසිලනකාරක ප්රවාහය:
හේතුව:ඇඹරුම් කලාපයට ප්රමාණවත් සිසිලනකාරක ප්රවාහයක් නොමැතිකම තාපය ගොඩනැගීමට සහ කම්පන වලට හේතු විය හැක.
විසඳුමක්:නිසි සිසිලනය සහතික කිරීම සඳහා සිසිලන සැපයුම් පද්ධතිය ප්රශස්ත කරන්න. ඵලදායී සිසිලනය තාප ප්රසාරණය සහ හැකිලීමේ අවදානම අඩු කරයි, එය කම්පන වලට හේතු විය හැක.
මෙවලම් දරන්නාගේ ගැටළු:
හේතුව:මෙවලම් රඳවනයේ හෝ ස්පින්ඩල් අතුරුමුහුණතේ ගැටළු නිසා කම්පන ඇති විය හැක.
විසඳුමක්:මෙවලම් රඳවනය ආරක්ෂිතව සවි කර ඇති බවත් ස්පින්ඩලය සමඟ නිසි ලෙස පෙළගස්වා ඇති බවත් සහතික කර ගන්න. කම්පන අවම කිරීම සඳහා උසස් තත්ත්වයේ සහ නිසි ලෙස නඩත්තු කරන ලද මෙවලම් රඳවනයන් භාවිතා කරන්න.
යන්ත්ර පදනම:
හේතුව:දුර්වල යන්ත්ර අත්තිවාරම හෝ ප්රමාණවත් ආධාරකයක් නොමැතිකම කම්පන විස්තාරණය කළ හැකිය.
විසඳුමක්:ඇඹරුම් යන්ත්රය ස්ථාවර සහ නිසි ලෙස නිර්මාණය කරන ලද අත්තිවාරමක් මත ස්ථාපනය කර ඇති බවට වග බලා ගන්න. යන්ත්රයට සම්ප්රේෂණය වන කම්පන අවම කිරීම සඳහා ඕනෑම ව්යුහාත්මක ගැටළු විසඳන්න.
ඇඹරීමේදී කම්පන ගැටළු ඵලදායී ලෙස විසඳීම සඳහා නිසි යන්ත්ර නඩත්තුව, රෝද තෝරා ගැනීම සහ වැඩ කොටස් හැසිරවීම යන දෙකෙහිම එකතුවක් අවශ්ය වේ. ක්රියාකරුවන් විසින් ගැටළු හඳුනාගෙන ඉක්මනින් විසඳීම සඳහා නිතිපතා පරීක්ෂණ සහ නඩත්තු පිළිවෙත් ක්රියාත්මක කළ යුතු අතර, එමඟින් ඇඹරුම් කාර්ය සාධනය සහ ගුණාත්මකභාවය වැඩිදියුණු වේ.
ඇඹරීමේදී පැටවීමේ ගැටළු
ඇඹරීමේදී පැටවීම යනු ඇඹරුම් රෝදයේ උල්ෙල්ඛ ධාන්ය අතර අවකාශයන් ඇඹරෙන ද්රව්ය වලින් පිරී යාමේ සංසිද්ධියයි, එහි ප්රතිඵලයක් ලෙස කැපුම් ක්රියාව අඩු වී ඝර්ෂණය වැඩි වේ. පැටවීම ඇඹරුම් ක්රියාවලියේ කාර්යක්ෂමතාවයට සහ ගුණාත්මක භාවයට අහිතකර ලෙස බලපෑ හැකිය. පැටවීමේ ගැටළු විසඳීමට ඇති විය හැකි හේතු සහ විසඳුම් මෙන්න:
මෘදු වැඩ කොටස් ද්රව්ය:
හේතුව:මෘදු ද්රව්ය ඇඹරීමෙන් උල්ෙල්ඛ ධාන්ය වේගයෙන් අවහිර විය හැක.
විසඳුමක්:මෘදු ද්රව්ය මත වැඩ කරන විට රළු ඇඹරුම් සහ විවෘත ව්යුහයක් සහිත ඇඹරුම් රෝදයක් භාවිතා කරන්න. මෙය ඉක්මනින් පැටවීම වැළැක්වීමට සහ කාර්යක්ෂම චිප් ඉවත් කිරීමට ඉඩ සලසයි.
ද්රව්ය දූෂණය:
හේතුව:වැඩ කොටසෙහි අඩංගු තෙල්, ග්රීස් හෝ සිසිලන අපද්රව්ය වැනි දූෂක ද්රව්ය පැටවීමට දායක විය හැක.
විසඳුමක්:අපවිත්ර ද්රව්ය ඉවත් කිරීම සඳහා ඇඹරීමට පෙර වැඩ කොටස නිසි ලෙස පිරිසිදු කිරීම සහතික කරන්න. පැටවීම අවම කිරීම සඳහා සුදුසු කැපුම් තරල හෝ සිසිලනකාරක භාවිතා කරන්න.
වැරදි සිසිලනකාරක යෙදුම:
හේතුව:සිසිලනකාරකය ප්රමාණවත් නොවීම හෝ නුසුදුසු ලෙස යෙදීම නිසා ප්රමාණවත් ලිහිසිකරණයක් සහ සිසිලනයක් නොලැබෙන අතර එමඟින් එය පැටවීමට හේතු විය හැක.
විසඳුමක්:සිසිලනකාරක ප්රවාහය සහ සාන්ද්රණය ප්රශස්ත කරන්න. සිසිලනකාරකය ඇඹරුම් කලාපයට ඵලදායී ලෙස ළඟා වී ක්රියාවලිය ලිහිසි කර සිසිල් කිරීම, පැටවීම වළක්වයි.
ප්රමාණවත් නොවන රෝද තියුණු බව:
හේතුව:අඳුරු හෝ ගෙවී ගිය ඇඹරුම් රෝදවල කැපුම් කාර්යක්ෂමතාව නැති වන බැවින් ඒවා පැටවීමට වැඩි ප්රවණතාවක් ඇත.
විසඳුමක්:ඇඹරුම් රෝදයේ තියුණු බව පවත්වා ගැනීම සඳහා නිතිපතා එය ඇඳ මුවහත් කරන්න. නැවුම් උල්ෙල්ඛ ධාන්ය නිරාවරණය කිරීමට සහ කැපුම් ක්රියාව වැඩි දියුණු කිරීමට රෝද ඇඳුමක් භාවිතා කරන්න.
අඩු රෝද වේගය:
හේතුව:අඩු වේගයකින් ඇඹරුම් රෝදය ක්රියාත්මක කිරීමෙන් චිප්ස් ඉවත් කිරීමට ප්රමාණවත් කේන්ද්රාපසාරී බලයක් නොලැබිය හැකි අතර, එය පැටවීමට හේතු වේ.
විසඳුමක්:නිශ්චිත රෝදය සහ වැඩ කොටස සංයෝජනය සඳහා නිර්දේශිත වේගයට ඇඹරුම් යන්ත්රය ක්රියාත්මක වන බවට වග බලා ගන්න. වැඩි වේගයන් වඩා හොඳ චිප් ඉවත් කිරීමට උපකාරී වේ.
අධික පීඩනය:
හේතුව:ඇඹරීමේදී අධික පීඩනයක් යෙදීමෙන් ද්රව්ය රෝදයට බලහත්කාරයෙන් ඇතුළු විය හැකි අතර එමඟින් බර පැටවීමට හේතු වේ.
විසඳුමක්:මධ්යස්ථ සහ ස්ථාවර ඇඹරුම් පීඩනයක් භාවිතා කරන්න. බර පැටවීමට තුඩු දෙන අධික පීඩනයකින් තොරව රෝදය කාර්යක්ෂමව කැපීමට ඉඩ සලසන පරිදි පෝෂක අනුපාතය සකස් කරන්න.
වැරදි රෝද පිරිවිතර:
හේතුව:ඇඹරීමට නියමිත ද්රව්ය සඳහා වැරදි පිරිවිතරයන් සහිත ඇඹරුම් රෝදයක් භාවිතා කිරීම පැටවීමට හේතු විය හැක.
විසඳුමක්:නිශ්චිත යෙදුම සඳහා සුදුසු උල්ෙල්ඛ වර්ගය, ග්රිට් ප්රමාණය සහ බන්ධනය සහිත ඇඹරුම් රෝදයක් තෝරන්න. රෝදය ද්රව්යයට ගැලපීම පැටවීම වැළැක්වීමට උපකාරී වේ.
ප්රමාණවත් නොවන සිසිලනකාරක පිරිසිදු කිරීම:
හේතුව:දූෂිත හෝ පැරණි සිසිලනකාරකය පැටවීමේ ගැටළු වලට දායක විය හැක.
විසඳුමක්:දූෂක සමුච්චය වීම වැළැක්වීම සඳහා නිතිපතා සිසිලනකාරකය පිරිසිදු කර ප්රතිස්ථාපනය කරන්න. නැවුම් සහ පිරිසිදු සිසිලනකාරකය ලිහිසි කිරීම සහ සිසිලනය වැඩි දියුණු කරයි, පැටවීමේ සම්භාවිතාව අඩු කරයි.
නුසුදුසු ඇඳුම් ඇඳීමේ තාක්ෂණය:
හේතුව:ඇඹරුම් රෝදය වැරදි ලෙස ඇඳීම අක්රමිකතා සහ පැටවීමට හේතු විය හැක.
විසඳුමක්:සුදුසු ඇඳුම් ඇඳීමේ මෙවලම භාවිතයෙන් රෝදය නිසි ලෙස අඳින්න. පැටවීම වැළැක්වීම සඳහා රෝද පැතිකඩ අනුකූල බවත් අක්රමිකතා වලින් තොර බවත් සහතික කර ගන්න.
පැටවීමේ ගැටළු ඵලදායී ලෙස විසඳීම සඳහා නිසි රෝද තේරීම, යන්ත්ර සැකසුම සහ නඩත්තු පිළිවෙත්වල එකතුවක් ඇතුළත් වේ. ක්රියාකරුවන් නිර්දේශිත ක්රියා පටිපාටි අනුගමනය කළ යුතුය, සුදුසු ඇඹරුම් පරාමිතීන් භාවිතා කළ යුතුය, සහ පැටවීම අවම කිරීමට සහ ඇඹරුම් කාර්ය සාධනය ප්රශස්ත කිරීමට නිතිපතා රෝද ඇඳීම ක්රියාත්මක කළ යුතුය.
විවිධ ලෝහ වැඩ සහ නිෂ්පාදන යෙදුම්වල ප්රශස්ත ප්රතිඵල ලබා ගැනීම සඳහා නිවැරදි ඇඹරුම් තැටිය තෝරා ගැනීම ඉතා වැදගත් වේ. තේරීම වැඩ කරන ද්රව්ය, අපේක්ෂිත නිමාව සහ භාවිතා කරන ඇඹරුම් යන්තයේ වර්ගය වැනි සාධක මත රඳා පවතී.
නිවැරදි ඇඹරුම් තැටිය තෝරා ගැනීම
ද්රව්ය අනුකූලතාව:
ෆෙරස් ලෝහ (වානේ, යකඩ):ෆෙරස් ලෝහ සඳහා විශේෂයෙන් නිර්මාණය කර ඇති ඇඹරුම් තැටි භාවිතා කරන්න. මෙම තැටි බොහෝ විට වානේවල දෘඪතාවයට සුදුසු උල්ෙල්ඛ අඩංගු වන අතර බර පැටවීමට ඇති ඉඩකඩ අඩුය.
ෆෙරස් නොවන ලෝහ (ඇලුමිනියම්, පිත්තල):අවහිර වීම වැළැක්වීම සඳහා මෘදු ලෝහ සඳහා සුදුසු උල්ෙල්ඛ සහිත තැටි තෝරන්න. ඇලුමිනියම් ඔක්සයිඩ් හෝ සිලිකන් කාබයිඩ් තැටි පොදු තේරීම් වේ.
උල්ෙල්ඛ ද්රව්ය:
ඇලුමිනියම් ඔක්සයිඩ්:ෆෙරස් ලෝහ මත සාමාන්ය කාර්ය ඇඹරීමට සුදුසු ය. එය කල් පවතින හා බහුකාර්ය වේ.
සර්කෝනියා ඇලුමිනා:ඉහළ කැපුම් කාර්යක්ෂමතාවයක් සහ කල්පැවැත්මක් ලබා දෙන අතර, ෆෙරස් සහ ෆෙරස් නොවන ලෝහ මත ආක්රමණශීලී ඇඹරීමට සුදුසු වේ.
සිලිකන් කාබයිඩ්:ෆෙරස් නොවන ලෝහ සහ ගල් ඇඹරීමට වඩාත් සුදුසුය. එය ඇලුමිනියම් ඔක්සයිඩ් වලට වඩා තියුණු නමුත් කල් පවතින බව අඩුය.
දැලක ප්රමාණය:
රළු ග්රිට් (24-36):වේගවත් කොටස් ඉවත් කිරීම සහ අධික බර ඇඹරීම.
මධ්යම ග්රිට් (40-60):කොටස් ඉවත් කිරීම සහ මතුපිට නිමාව තුලනය කරයි.
සියුම් ග්රිට් (80-120):මතුපිට සකස් කිරීම සහ සැහැල්ලු ඇඹරීම සඳහා සුදුසු, සුමට නිමාවක් සපයයි.
රෝද වර්ගය:
27 වර්ගය (අවපීඩන මධ්යස්ථානය):මතුපිට ඇඹරීමට සහ දාර වැඩ සඳහා කදිම, පැතලි මතුපිටක් සහිත සම්මත ඇඹරුම් තැටිය.
වර්ගය 29 (කේතුකාකාර):ආක්රමණශීලී කොටස් ඉවත් කිරීම සහ වඩා හොඳ මතුපිට මිශ්ර කිරීම සඳහා කෝණික නිර්මාණය.
1 වර්ගය (කෙළින්):කැපුම් යෙදුම් සඳහා භාවිතා වේ. එය නිවැරදි කැපීම සඳහා තුනී පැතිකඩක් සපයයි.
අයදුම්පත:
ඇඹරීම:ද්රව්ය ඉවත් කිරීම සහ හැඩගැස්වීම සඳහා සම්මත ඇඹරුම් තැටි.
කැපීම:ලෝහ කැපීම සඳහා කැපූ රෝද භාවිතා කරන්න, සෘජු සහ පිරිසිදු දාරයක් ලබා දෙන්න.
ෆ්ලැප් තැටි:ඇඹරීම සහ නිම කිරීම එකකින් ඒකාබද්ධ කරන්න. මතුපිට මිශ්ර කිරීම සහ සුමට කිරීම සඳහා සුදුසු වේ.
ඇඹරුම් යන්තය සමඟ අනුකූලතාව:
ඇඹරුම් තැටිය භාවිතා කරන ඇඹරුම් යන්තයේ වර්ගය සහ වේගය සමඟ අනුකූල වන බවට වග බලා ගන්න. තැටියේ උපරිම RPM (මිනිත්තුවකට විප්ලව) සඳහා නිෂ්පාදකයාගේ නිර්දේශ පරීක්ෂා කරන්න.
කාර්යයේ විශේෂත්වය:
අධික තොග ඉවත් කිරීම:කාර්යක්ෂම ද්රව්ය ඉවත් කිරීම සඳහා රළු ග්රිට් එකක් සහ 27 හෝ 29 වර්ගයේ තැටියක් තෝරන්න.
මතුපිට නිමාව:සුමට නිමාවක් සඳහා ෆ්ලැප් තැටි සහිත මධ්යම සිට සියුම් ඇඹරුම් තෝරා ගන්න.
ආරක්ෂක සලකා බැලීම්:
ආරක්ෂිත කණ්නාඩි සහ අත්වැසුම් වැනි සුදුසු පුද්ගලික ආරක්ෂක උපකරණ (PPE) පැළඳීම ඇතුළුව ආරක්ෂක මාර්ගෝපදේශ අනුගමනය කරන්න.
වැඩි කල්පැවැත්ම සහ ආරක්ෂාව සඳහා ශක්තිමත් කරන ලද තැටි තෝරන්න.
වෙළඳ නාමය සහ ගුණාත්මකභාවය:
ගුණාත්මකභාවය සහ අනුකූලතාව සඳහා ප්රසිද්ධ කීර්තිමත් වෙළඳ නාමවලින් තැටි තෝරන්න. උසස් තත්ත්වයේ තැටි වඩා හොඳ කාර්ය සාධනයක් සහ කල්පැවැත්මක් ලබා දෙයි.
පිරිවැය සලකා බැලීම:
ඇඹරුම් තැටියේ අපේක්ෂිත ආයු කාලය සහ කාර්ය සාධනය සමඟ ආරම්භක පිරිවැය තුලනය කරන්න. උසස් තත්ත්වයේ තැටිවලට ඉහළ මූලික පිරිවැයක් තිබිය හැකි නමුත් කාලයත් සමඟ වඩා හොඳ වටිනාකමක් ලබා දිය හැකිය.
මෙම සාධක සලකා බැලීමෙන්, ක්රියාකරුවන්ට ඔවුන්ගේ නිශ්චිත යෙදුම් සඳහා නිවැරදි ඇඹරුම් තැටිය තෝරා ගත හැකි අතර, කාර්යක්ෂමතාව, ආරක්ෂාව සහ ප්රශස්ත ප්රතිඵල සහතික කෙරේ.
නිගමනය
අවසාන වශයෙන්, සුදුසු ඇඹරුම් තැටිය තෝරා ගැනීම සාර්ථක ලෝහ වැඩ සහ නිෂ්පාදන ප්රතිඵල ලබා ගැනීමේ තීරණාත්මක අංගයකි. තේරීම වැඩ කරනු ලබන ද්රව්ය, අපේක්ෂිත නිමාව සහ භාවිතයේ ඇති ඇඹරුම් යන්ත වර්ගය වැනි විවිධ සාධක මත රඳා පවතී. ද්රව්ය අනුකූලතාව, උල්ෙල්ඛ වර්ගය, ග්රිට් ප්රමාණය, රෝද වර්ගය, යෙදුම, ඇඹරුම් යන්ත අනුකූලතාව, කාර්ය නිශ්චිතභාවය, ආරක්ෂාව, වෙළඳ නාම ගුණාත්මකභාවය සහ පිරිවැය සලකා බැලීමෙන්, ක්රියාකරුවන්ට ඔවුන්ගේ ඇඹරුම් ක්රියාවලීන්හි කාර්යක්ෂමතාව සහ ආරක්ෂාව වැඩි දියුණු කිරීම සඳහා දැනුවත් තීරණ ගත හැකිය.
ආරක්ෂිත මාර්ගෝපදේශ පිළිපැදීම, සුදුසු පුද්ගලික ආරක්ෂක උපකරණ පැළඳීම සහ ඇඹරුම් යන්ත සහ තැටි අනුකූලතාව සඳහා නිෂ්පාදක නිර්දේශ අනුගමනය කිරීම අත්යවශ්ය වේ. එය අධික තොග ඉවත් කිරීම, මතුපිට නිම කිරීම හෝ කැපුම් යෙදුම් සඳහා වේවා, නිවැරදි ඇඹරුම් තැටිය කාර්යයේ ගුණාත්මකභාවය සහ කාර්යක්ෂමතාවයට සැලකිය යුතු ලෙස බලපෑ හැකිය.
මීට අමතරව, ගෙවී යාම සහ ඉරී යාම සඳහා වරින් වර පරීක්ෂා කිරීම, අධික උනුසුම් වීම සහ කම්පන ගැටළු වැනි ගැටළු විසඳීම සහ පැටවීමේ ගැටළු තේරුම් ගැනීම ඇඹරුම් තැටියේ ආයු කාලය දීර්ඝ කිරීමට සහ ස්ථාවර ක්රියාකාරිත්වය සහතික කිරීමට දායක වේ.
සාරාංශයක් ලෙස, ඇඹරුම් තැටි තෝරා ගැනීම, භාවිතා කිරීම සහ නඩත්තු කිරීම සඳහා හොඳින් දැනුවත් සහ ක්රමානුකූල ප්රවේශයක් ප්රශස්ත ප්රතිඵල ලබා ගැනීම, ඵලදායිතාව වැඩි දියුණු කිරීම සහ ආරක්ෂිත වැඩ පරිසරයක් සහතික කිරීම සඳහා යතුරයි.
පළ කිරීමේ කාලය: ජනවාරි-12-2024